在特斯拉宣布一體壓鑄技術(shù)取得新突破之后,全球銷冠汽車公司豐田近日也公開(kāi)了其開(kāi)發(fā)的車身一體壓鑄成型技術(shù)。豐田表示,該技術(shù)旨在進(jìn)一步降低生產(chǎn)工序和成本,從而在難以通過(guò)傳統(tǒng)制造方式盈利的電動(dòng)車領(lǐng)域提高利潤(rùn)。
據(jù)豐田方面介紹,在使用一體壓鑄技術(shù)之前,一個(gè)完整的車身后部需要約86個(gè)不同的零部件,并且需要經(jīng)過(guò)33個(gè)獨(dú)立的工序來(lái)組裝。這一復(fù)雜的過(guò)程通常需要數(shù)小時(shí)來(lái)完成,在應(yīng)用一體壓鑄工藝后,車身后部只需一個(gè)單一的零部件和一個(gè)簡(jiǎn)單的工序。豐田計(jì)劃進(jìn)一步縮短時(shí)間,將工序縮短至約3分鐘。
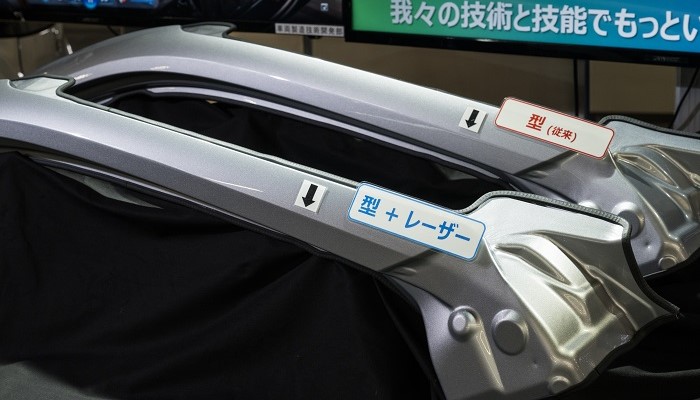
該技術(shù)在結(jié)構(gòu)更加復(fù)雜的車身前部提升更加明顯——豐田表示,傳統(tǒng)的制造方法需要用到91個(gè)零部件,并且要經(jīng)過(guò)51個(gè)工序。而使用一體壓鑄技術(shù)后,零部件和工序同樣可以簡(jiǎn)化為一個(gè)單一的零部件和一個(gè)工序。
這一制造流程進(jìn)步盡管相較傳統(tǒng)流程已經(jīng)具有明顯進(jìn)步,但仍落后于特斯拉。據(jù)特斯拉最新曝光的一體壓鑄工藝相關(guān)信息顯示,目前特斯拉已經(jīng)具備將幾乎所有車身底部零部件整合壓鑄,這將幫助特斯拉再次減半其生產(chǎn)成本。
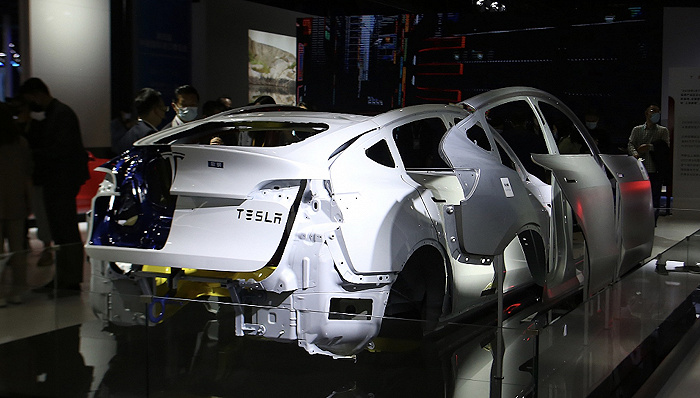
另一方面,通過(guò)在測(cè)試模具上使用3D打印機(jī),特斯拉同樣在車輛開(kāi)發(fā)領(lǐng)域具備成本優(yōu)勢(shì)。相關(guān)消息人士表示,通過(guò)在設(shè)計(jì)驗(yàn)證領(lǐng)域應(yīng)用該方法,可使模型成本降低至傳統(tǒng)金屬模型的僅3%。
為盡量加快抹平特斯拉在制造成本方面取得的優(yōu)勢(shì),豐田同時(shí)改變了其生產(chǎn)方式。在豐田愛(ài)知本町工廠,豐田部分實(shí)施了一種不依賴傳送帶的生產(chǎn)方式。
據(jù)豐田介紹,完成組裝的車輛在工廠內(nèi)通過(guò)傳感器識(shí)別和有限自動(dòng)駕駛技術(shù)來(lái)完成點(diǎn)到點(diǎn)的運(yùn)輸。這在降低產(chǎn)線投資的同時(shí),也使得豐田能夠在短時(shí)間內(nèi)變更其工廠內(nèi)部配置。
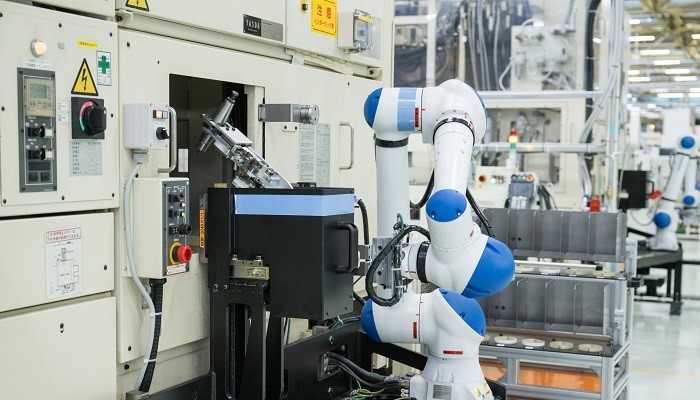
經(jīng)過(guò)對(duì)電動(dòng)化轉(zhuǎn)型舉棋不定的十年后,豐田正在加速追趕特斯拉的腳步。除領(lǐng)近期曝光的生產(chǎn)工藝改良和一體化壓鑄工藝的應(yīng)用,豐田在今年7月公布了對(duì)固態(tài)電池的重大技術(shù)突破;此外,通過(guò)對(duì)生成式AI技術(shù)的應(yīng)用,豐田有望在車型開(kāi)發(fā)過(guò)程中加快工作效率。
數(shù)據(jù)顯示,特斯拉2022年的全球銷量約131萬(wàn)輛,而豐田純電動(dòng)車的銷量?jī)H為2.4萬(wàn)輛。不過(guò),在對(duì)電池技術(shù)完成突破、應(yīng)用AI、一體壓鑄和自動(dòng)駕駛等技術(shù)后,豐田希望快速追趕特斯拉的銷量——該公司希望到2026年完成純電車型年銷150萬(wàn)輛的成績(jī),這一數(shù)字是2022年銷量的60倍以上。