界面新聞實習記者 | 羅容
倒置的塑料瓶被固定在呈螺旋狀排列的流水線上,高壓水流經由瓶口,正自下而上清洗著塑料瓶內壁。完成這道工序后,塑料瓶被翻轉朝上,傳送到下一環節等待注入飲料。完成加蓋、打碼等流程后,一瓶500毫升裝的可口可樂就誕生了。
在位于杭州經濟技術開發區的浙江太古可口可樂飲料有限公司(下稱浙江工廠),一條這樣的流水線每秒就能生產出6瓶可口可樂。
“過去兩年,太古可口可樂凈生產線效率提升超過4%。”9月8日,太古可口可樂(中國)有限公司技術總監駱超向實地探訪浙江工廠的界面新聞記者表示。別小看了這個數字,對于一家總計擁有100條生產線的企業來說,意味著可以減少四條生產線的投入。
太古可口可樂是可口可樂公司全球銷量第五大的裝瓶合作伙伴。該公司旗下的浙江工廠始建于1996年,擔負著浙江省大部分地區可口可樂系列產品的生產和銷售,年銷售額逾30億元。
提高可口可樂生產線的效率,也同時意味著工廠能耗的降低。減少一條生產線的投入,每年可因此節省500萬-800萬度電的能源消費。對于浙江工廠而言,這個數字相當可觀。
可作為類比的是,該工廠已在屋頂完成了占地2萬平方米的光伏板鋪設,年發電量可達到60萬度。但與節省一條生產線所帶來的節能收益相比,僅相當于其十分之一。
而這一切,主要歸功于2021年3月部署在浙江工廠的西門子制造信息系統(MIS),該系統由西門子和太古可口可樂聯合開發。通過對產線的數字化監控,這套系統能夠及時排查出故障設備,減少損失和停機率,并通過能源管理模塊,計算出能耗數據,從中找到提升生產線效率的機會點。
浙江工廠工程經理劉繼舉例稱,在部署MIS后,飲料生產過程中的溫度數據得以實時抓取。如果發現冷卻水的溫度已足夠低,可以通過控制自動化閥門等措施減少冷卻水的流量,從而降低冷卻設備的能耗。冷卻水的作用,是降低生產過程中可口可樂的溫度。利用這一細微調整,浙江工廠生產線平均每年就可節省約10萬度電。
MIS目前已部署到太古可口可樂17家工廠的43條產線,由此帶來的生產線改進和調整,太古可口可樂全系統的生產能耗在過去兩年降低了8%,平均每年節約5000萬度電。
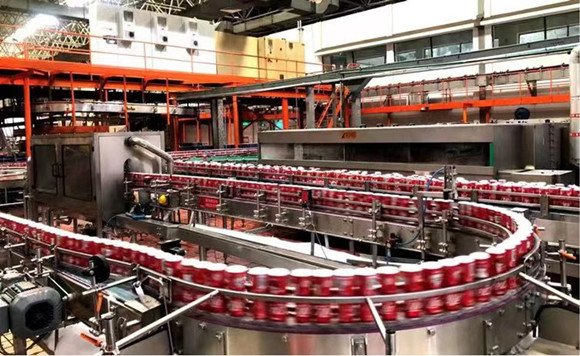
有賴于此,太古可口可樂工廠核心業務的碳排放量與2018年相比降低了24%,預計2030年將進一步降低70%。為此,其已計劃今年將MIS系統的應用范圍擴大至26家工廠的75條產線。
浙江工廠也并未停下在屋頂鋪設光伏的腳步,目前工廠正在進行光伏項目的二期施工,預計裝機容量將在現有基礎上增長150%。
距離浙江工廠逾175公里的大同齒輪傳動(昆山)股份有限公司(下稱大同齒輪),同樣為降碳目標動起了在屋頂安裝光伏的打算。
截至去年底,該工廠屋頂光伏板的覆蓋率達到62%,年均發電量200萬度,占其總用電量的27%。大同齒輪2000年在當地建廠,主營機加工件產品,其客戶名單中就包括西門子。
除了在屋頂鋪上光伏板,大同齒輪還于2022年引入了西門子推出的碳足跡可信精算與追溯解決方案(SiGREEN),以實現節能降碳的目標。
SiGREEN的一項重要功能,是計算企業的碳足跡,指導其有效地進行能源效率提升,進而降低碳排放。這套系統的引入,讓大同齒輪總經理許正忠有了不少意外發現。
“我們最初跟西門子討論接入SiGREEN時,考慮的是計算工廠最重要的設備碳排放,并沒有打算統計非重點小型設備碳排放,但一些小型設備的能源使用數據讓我們嚇了一跳。”許正忠告訴界面新聞記者。
根據SiGREEN的統計,大同齒輪廠房頂部所安裝的每臺巨型節能風扇,一天的用電量為20度,而一臺落地風扇的用電量遠大于此,通常只供一位工人使用。“有了準確的數據做佐證,我們決定將工廠年內落地風扇數量減少90%。”許正忠稱。
現在,廠房頂部不停轉動的巨型節能風扇已經替代空調,成為大同齒輪廠區內通風降溫的主要途徑。在層高11.5米的廠房內,還有三排敞開的天窗,保證車間內的自然采光和空氣流通。
大同齒輪此前也曾嘗試在廠房內安裝空調,但許正忠將其形容為一次失敗的經驗。“因為空調沒有辦法把廠區內的熱氣排出去,造成它根本發揮不了降溫的作用。”他解釋說。
根據SiGREEN的統計,空調也是大同齒輪夏天耗電量的最大來源。但在空間廣闊的廠區內,空調無法把溫度降到一定的體感舒適度,并非為工廠降溫的高性價比選項。